Rugged IoT Gateway Optmize Wind Turbine Communication Reliability
2015-10-13
Product Solutions |
V2201 Series
Fanless, ultra-compact and rugged x86 industrial IoT embedded computer |
|
For a wind farm, maximizing power output is obviously critically important. A powerful and reliable industrial computing platform is one of the keys to ensuring efficient power generation—together with advanced software to control the wind turbine and respond to changes in wind speed and direction.
The computing platform has three important tasks in wind power generation:
1. Pre-process the data to filter garbage information and only send useful information back to the control center. This makes the best use of control center resources, and also ensures timely delivery of data by reducing bandwidth demands.
2. Constantly monitor critical devices’ status to ensure they are functioning correctly. This allows operators to take appropriate steps at an early stage and avoid turbine downtime. In addition, if the computer detects an abnormal situation, it sends an alert, so that timely repair and maintenance can minimize losses.
3. Communicate in real-time with the remote control center, allowing the control center to adjust turbine blade pitch angles and other parameters according to changes in wind speed and other conditions.
To execute these tasks accurately and efficiently, the computing platform needs to offer strong computing performance, diverse communication capabilities, and great reliability. This combination of features ensures that all data from multiple devices can be processed and sent to the control center in time.
As problems sometimes go unnoticed by regular visual inspections, when problems occur, a sensor detects the first signs of potential damage and the computer sends a message to the control center. This warning allows maintenance staff to take appropriate steps at an early stage and to avoid turbine failure. For serious issues, an alert sent to the control center in real time allows staff to shut down the turbine immediately, avoiding blade damage.
Realizing the industrial internet of things (IIoT) concept, wind turbine farms feature a multitude of devices connected internally and externally by an intelligent computing platform. Onboard industrial computers allow all wind turbines within a farm to communicate with each other, sharing data to adjust direction and speed. A wind turbine not only adjusts its direction and speed based on the weather, but also accounting for the behavior of other wind turbines. This approach maximizes power generation efficiency without requiring human supervision. The IIoT concept also adds redundancy and fault tolerance—if a wind turbine is unable to communicate with the control center directly, it can send its message via one of the other wind turbines in the farm.
Wired connections are usually used inside each wind turbine on a farm to link them to an Ethernet LAN that connects all the towers to a remote control station. However fully-wired communications solutions are not always feasible or cost-effective, for example, on an offshore wind farm. As a result, some system integrators also use redundant wireless connections to reduce deployment costs.
Since wind turbines are usually sited in remote areas, all components need to face the varying challenges of the local climate, year-round. The continual vibration caused by normal operations is another challenge to reliability. Choosing rugged industrial-grade devices ensures lower costs and maximizes profits.
System Requirements
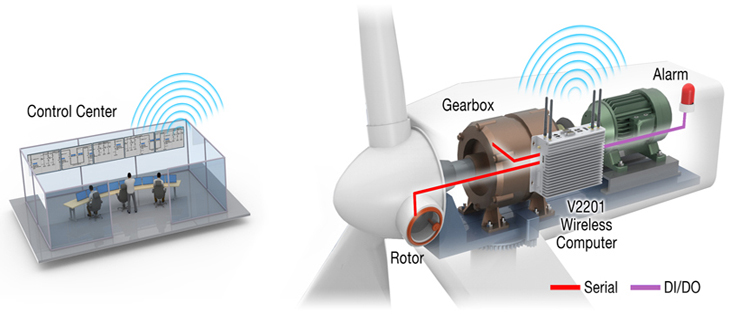
• Rugged design to withstand harsh environmental conditions and continual vibration, thereby reducing downtime.
• A variety of communication interfaces, such as LAN ports, Serial ports, DI/O ports, and wireless, allow the computer to be easily connected with diverse devices and nearby wind turbines. The system should also be able to send alerts to the control center and directly to the mobile devices of maintenance staff.
• High computing power to process, monitor and control important devices in the turbine, without interruption or lag.
• Small size to make it easier to install in constricted spaces.
Moxa Solution
Moxa’s new LTE-enabled V2201 wireless computers ensures reliable system operation in temperatures ranging from -40 to 70°C to help you avoid system crash or unstable situation from extreme temperature variation. The small palm size design (150 x 48.8 x 120.2 mm) is fanless, and support both DIN-rail and wall mounting capability, making installation and maintenance easy. The versatile communication infrastructure and storage expansion design allow users don’t need to worry that storage limitations and complex communication demand. Rugged, Flexible and wireless enabled make V2201 your most reliable partner in industrial IoT applications.
Why Moxa
• Wide-temperature tolerance from -40 to 85°C, and industrial grade anti-vibration and anti-shock design to keep the system running 24/7 in harsh environments.
• A variety of interfaces offers communications flexibility. They include: two serial ports, two LAN ports, and one pair of DI/DO ports.
• High computing power can handle real-time processing of the huge amount of complex data continuallyg enerated by sensors on the rotor, gears, and other devices.
• Various wireless communication options, and wireless redundancy capability to provide additional communication flexibility.
• Easy installation, because the unit is palm-sized (150 x 48.8 x 120.2 mm), and versatile design allows either DIN rail or wall-mounting.
|