Enabling Smart Manufacturing in the Era of Industry 4.0
The influx of technological advances over the past few years has impacted the manufacturing landscape tremendously, giving rise to the phenomenon commonly known as the smart factory. At the heart of the smart factory is data collection, relying heavily on the numerous sensors, motors, and robotics in production and assembly lines.
There is good reason why the smart factory is being touted as the future of manufacturing. Manufacturers increasingly have to deal with stiff global competition, shorter product cycles, and changing customer demands, which all add pressure on production schedules, efficiency, and profit margins. To improve flexibility, efficiency, and throughput, digital connectivity to enable data collection is key to achieve these goals. In this article, we focus on three aspects—mass customization, predictive maintenance, and remote monitoring—to illustrate the benefits of smart manufacturing for your shop floor.
Implementing Mass Customization
More and more modern-day consumers want products that are customized and available on demand, thus driving the shift towards mass customization in the manufacturing industry. What’s more, mass customization promises customers individually customized products at the price of mass-produced items. To accomplish mass customization, custom customer orders are intelligently integrated with Enterprise Resource Planning (ERP) systems or other smart applications, and mapped with the inventory system so upstream materials can be ordered if necessary. These systems and applications will then connect to the Advanced Planning & Scheduling System (APS) and MES/SCADA systems to initiate standardization, mass production, custom production, and mixed model production.
Mass customization is achieved through smart production lines comprised of several heterogeneous smart machines to support both standardized and customized products. By connecting factory equipment to smart sensors, PLC/edge computers, and the MES, shop-floor equipment can download user/OEM developed programs to execute intelligent procedures according to automated changeover commands. This results in minimal breaks in the production process so that business can continue.
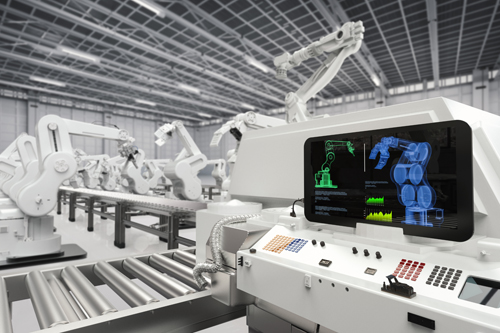
Generally speaking, the scenario in interconnected factories will entail serial device servers and wired or wireless industrial networking devices connected to factory equipment to extract data such as product ID. Then, networking hardware such as wireless access points and Ethernet switches are applied to transmit the information over to your MES/DNC (Direct Numerical Control) server. The MES/DNC sends changeover commands and G-Codes over the network to each connected factory machine. This process allows CNC machines and robots to download more information to become adaptive smart machines and carry out their jobs effectively.
An adaptive smart machine can perform changeovers on the fly and reconfigure itself with different production modules on the same base machine platform. It can adapt to constant size and format changes to reduce system downtime and increase production efficiency. By enabling this adaptive intelligence, production lines remain operational and continue to produce the next order. However, in a mixed production scenario, the MES must handle more coordination commands with limited computing capability. To alleviate this extra load, edge computers play the important role of handling the partial decision-making (of the production loop) of the MES. Edge computers reduce the communication latency, and any risks to production stops by autonomously running the entire production processes of the loop in case the MES connection drops off.
Predictive Maintenance and Real-time Monitoring
Self-monitoring is a built-in test (BIT) mechanism that allows machines to perform self-tests to discover whether it needs maintenance or repair. Typical tests are for temperature, current, voltage, (motor) torque, or communication quality, for example, the decreased torque output on a robot arm or overheating/vibration on a CNC motor. However, even after identifying potential issues, technician accessibility could be limited and checking problems on site during operational hours could be costly. Additionally, managers on the enterprise-end of the business need systems online so they can monitor the operational performance of assets and their availability.
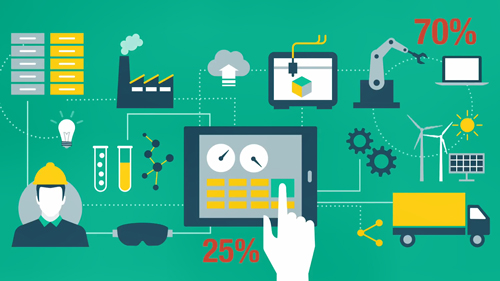
Collecting machine data and connecting systems to the cloud enables remote real-time monitoring and remote maintenance of your factory and machines. With full transparency to machine performance, system status, and more importantly hard data, managers are able to keep track of current machine performance. Operators can even see historical data on similar machines to predict performance variation outside the acceptable boundaries. With this abundance of data, software engineers are able to build a mathematic model based on per-alarm occurrences to predict machine failure so the operators can proactively schedule maintenance, improving the mean time to repair (MTTR) and saving significant profit loss from downtime and repair.
Combining this real-time information with remotely connected maintenance software also allows operators to service machines remotely before costly issues can occur, and with this knowledge they can have the technician scheduled to arrive outside peak operating hours to avoid downtime.
|